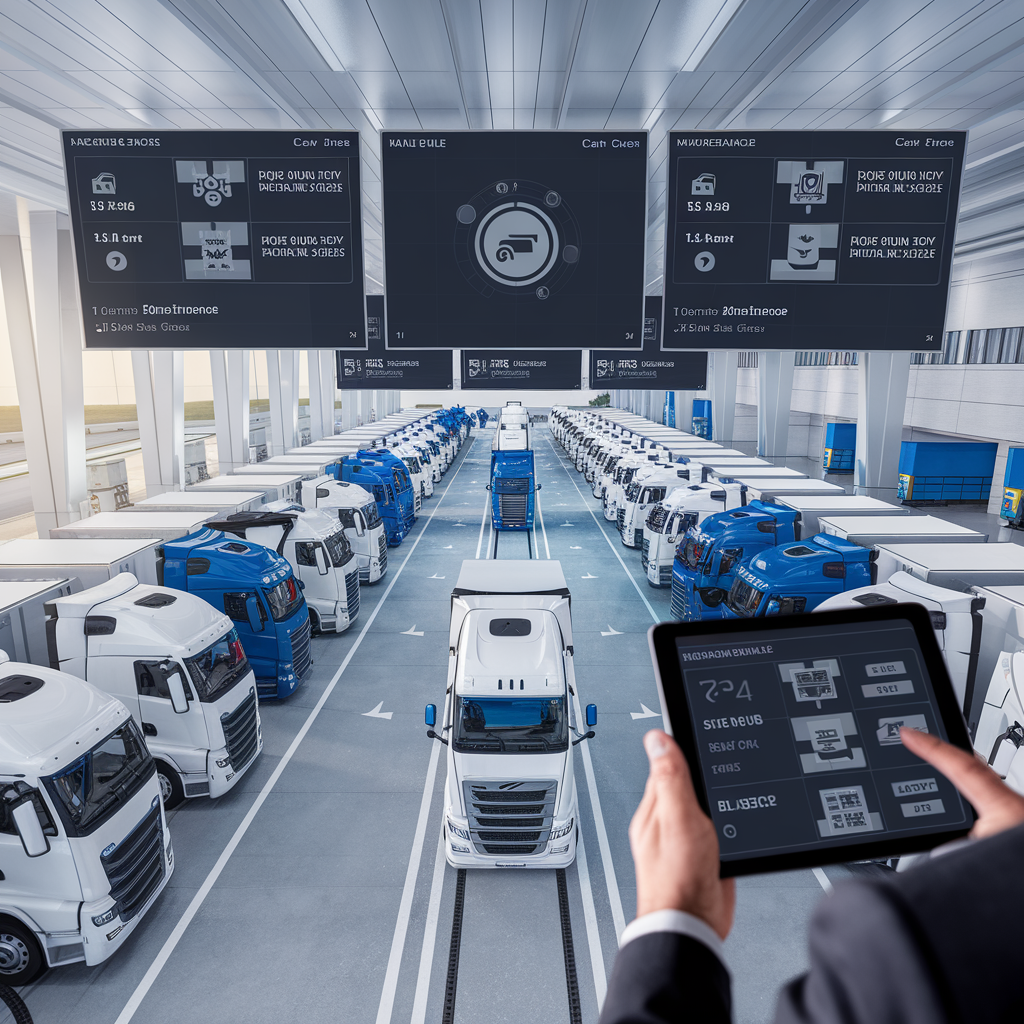
Truck Stop Dispatch Optimization
Imagine it’s rush hour, and truck stops everywhere are buzzing like hives. Dispatchers? They’re juggling driver schedules, fuel requests, maintenance needs—keeping all those moving pieces in check is no easy task. But what if there was a way to make it all simpler, to cut through the chaos and get each truck where it needs to go, faster and with fewer headaches? Let’s talk about dispatch optimization and how it can make life easier for dispatchers, drivers, and everyone else in the logistics chain.
What’s the Deal with Dispatch Optimization?
Truck stop dispatch optimization is all about making the best use of every minute and mile. Every truck sitting in a queue waiting for fuel or repairs means lost time and revenue. And every extra minute a driver spends hunting for parking is fuel wasted. The goal? Keep trucks moving efficiently, minimizing downtime so drivers can stay on the road and keep goods flowing.
Dispatch optimization isn’t just about having the right tools—it’s about using them in ways that fit the demands of a high-paced trucking schedule. Think of it like a game of chess: every truck, every driver, every mile is a move. And the best strategies come from looking several steps ahead.
The Core Challenges Dispatchers Face
Let’s get real about the challenges. Truck stops are like mini ecosystems, each with its own needs and quirks. Here’s a look at some of the main issues dispatchers have to wrestle with every day:
Crowded Parking Lots: Every night, thousands of drivers search for a spot to park. When spots are scarce, drivers waste precious time looking, often forced to settle for inconvenient or even unsafe locations.
Maintenance Coordination: Trucks are machines, and machines break down. But coordinating repairs in a way that doesn’t disrupt schedules? That’s a tough act to juggle.
Fueling Efficiency: Imagine trying to keep 20 trucks fueled with just four pumps. Keeping things moving smoothly requires timing and smart scheduling to avoid bottlenecks.
Each of these challenges on its own is a handful. Together, they make every shift a delicate balancing act. But with the right optimization strategies, dispatchers can get a leg up on all three fronts.
The Power of Real-Time Data
The secret sauce in dispatch optimization? Real-time data. Imagine having up-to-the-second info on everything happening at a truck stop—from which pumps are free to which maintenance bays have a short wait. It’s like having a crystal ball, allowing dispatchers to make decisions based on what’s actually happening, not what they hope will happen.
Real-time data means dispatchers aren’t flying blind. Instead, they have a clear view of each driver’s location, status, and estimated time of arrival. This makes it much easier to coordinate who gets serviced first, who’s next in line, and who can be rerouted to another nearby stop if things get too congested.
Dynamic Scheduling: The Key to Smooth Operations
Here’s where dynamic scheduling comes into play. Picture it as the ability to shuffle and reshuffle tasks as priorities change throughout the day. Maybe a driver reports a tire issue mid-shift, or perhaps a truck stop runs out of fuel earlier than expected. With dynamic scheduling, dispatchers can adapt, updating the queue so that downtime is minimized, and every driver stays on track.
For example, a driver headed to a stop with limited parking might be rerouted to one with more availability, saving time and reducing the stress of hunting for a spot. Similarly, if a maintenance team frees up early, another truck in need can be sent over right away. It’s all about making adjustments in real time, so everything runs smoothly.
Fueling Coordination: Cutting Down Idle Time
Fueling may sound simple, but when dozens of trucks are involved, even a small delay can become a big deal. And when trucks sit idling in line for fuel, they’re burning through profits with every passing minute. Optimizing dispatch means giving each driver a specific fueling window—like a dinner reservation. This way, they can pull in, fuel up, and be on their way without clogging up the line.
Automated fuel scheduling apps help track which drivers are approaching and when they’ll need a fill-up, eliminating guesswork. And by staggering those fueling times, there’s less overlap and fewer logjams.
Maintenance Coordination: Keeping Trucks in Top Shape Without Missing a Beat
Maintenance is a necessary evil in the trucking world. But scheduled maintenance is different from an unexpected breakdown, and both need different handling. Dispatch optimization means predicting maintenance needs based on each truck’s mileage, wear and tear, and recent performance data.
When it’s time for scheduled maintenance, dispatchers can plan around it, arranging for other trucks to fill in so the downtime doesn’t disrupt the day’s operations. And if there’s a surprise breakdown? With a bit of data and quick thinking, dispatchers can shuffle resources, ensuring that repairs happen with as little impact as possible on the schedule.
The Human Side of Optimization
It’s not all technology and timing, though. Dispatchers are the unsung heroes of the trucking industry. They’re the ones who smooth out the rough patches, balancing data-driven decisions with a personal touch. A quick check-in call to a tired driver, a reroute to a truck stop with better amenities—these little touches go a long way toward keeping morale high.
When you’re working with real people, every decision impacts someone’s day, their stress levels, and even their safety. That’s why dispatch optimization isn’t just about crunching numbers. It’s about creating an environment where drivers feel valued and supported, even on their toughest days.
The Bottom Line: Efficiency Without Compromise
In the fast-paced world of truck dispatch, time is money. By optimizing dispatch schedules, truck stops can reduce idle time, boost productivity, and keep drivers moving. But more than that, they can create an environment that respects drivers’ time and effort, valuing every mile they cover.
At the end of the day, dispatch optimization is a win-win. It makes the work easier for dispatchers and helps drivers focus on the road, knowing there’s a plan in place that’s got their back. So, next time you’re at a truck stop, take a moment to appreciate the well-oiled machine behind the scenes, keeping everything on track and rolling forward.
For further details, visit The American Truck Inc.
To schedule appointments, contact us for a complimentary consultancy session.